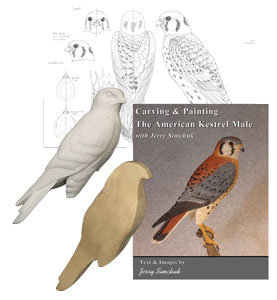
Many artists are discovering the beauty of chainsaw wood carving. The art is a natural extension their skill set. It often includes a combination traditional carving techniques and contemporary designs. Crager and his wife, Tracie Dugas, have carved beautiful wood creations since the 1960s. In between shows, they try to get home as much as possible to help out with painting and staining. His daughters now help him with staining and painting, as well. They also prefer to use white pine, which is lighter and less likely to crack.
Rich Anderson
Rich Anderson is a chainsaw wood carving artist from Reedsport. Anderson is a Poughkeepsie native and lives with his son and wife. Anderson holds several degrees in the fine arts and teaches art to children in the Pre-K to fifth grades. He has carved many sculptures around Long Island and has even created sculptures in Colorado. His work includes sculptures of standing trees and smaller pieces such as corn ears. He is currently working on a sign to Youngs Farm in Riverhead.
He is able to create exquisite sculptures using a $400 chainsaw, which would normally take several days to chisel a tree. Chainsaw wood carving can also be used to create beautiful sculptures that are more environmentally friendly than hammers and chisels. Anderson promotes his business by word of mouth. He has created a huge cobra and great blue heron to help a Wading River mechanic.
Tracie Dugas
Tracie Dugas has created a life-size Wizard from wood. This is a great example of her skill as an expert chainsaw wood carver. The 49-yearold lives in Clare Nova Scotia between Digby, Yarmouth. The chainsaw wood carver, was among many artists who showed their work during Canada Day weekend in Sydney. The Sydney waterfront was flooded with tourists, but the brief dry spell provided a perfect opportunity for locals to enjoy the waterfront and catch a glimpse of the chainsaw artist.
Tim Crager
Although Tim Crager wasn't an artist, and was only slightly skilled with a chainsaw at the time, his passion for carving became a full-time job six years ago. Since then, Crager has traveled the Eastern U.S., selling more than $1 million worth of carvings. Crager was born in Garrett, Eastern Kentucky. He grew up watching the chainsaw wood carver at his work. The artist's style captivated him, so one day he called his boss and put in his two-week notice.
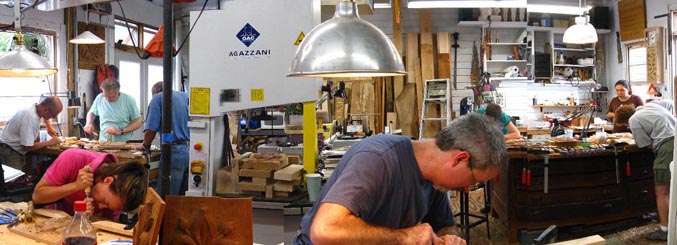
When it comes to material choice, Crager prefers white pine because it's easily available from tree trimming companies. Many people prefer different types of wood. Crager is a follower of the grain and allows the saw to guide his creations. Crager may know exactly what he's making before he starts any project. However, he often changes his mind mid-project. For small projects, it takes less than an hour. Large carvings can take 33 to 35hrs.
Don Scoggins
Don Scoggins, a chainsaw wood carver, is his name. His wood carvings feature intricate details and many animals. His creations attract attention from both neighbors and tourists. The chainsaw sculptures are so large and detailed that they adorn the entrance and coffee shop at Blue Arrow Farm. Blue Arrow Farm is run by Don Oriolo. He is also the owner and manager of Felix the Cat. Don Oriolo and his wife, Kacie, met while competing in a chainsaw competition at the New Jersey State Fair.
The 15-year-old wood carver and winner of the award was inspired to start carving at a Reedsport competition. He was already proficient at hand carving, but he hadn't ever used a machine like a chainsaw. His carvings include an otter and a mother bear, as well as a squirrel peeking through a tree. And now, he's ready to compete at the National Chainsaw Carving Competition.
Dan Porter
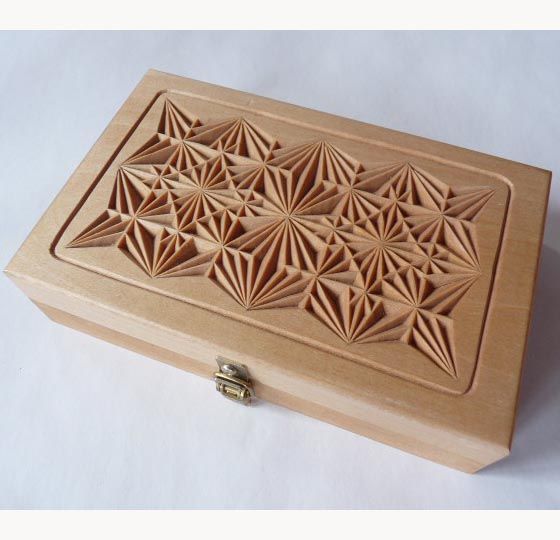
For many years, Dan Porter, a chainsaw wood carver from Oregon, has been a sought-after local talent. His intricate, detailed carvings have been admired all over the world. He was an accomplished wood carver who spent many years working in the lumber industry. These are just a few of the many things that made him a top-notch wood carver.
FAQ
Are there any tips for starting a woodworking enterprise?
Starting a woodworking business is a lot of work. It's worth it if you're passionate and willing to work hard. You will probably love the challenge of starting your own business.
One thing to keep in mind when launching a new venture is that you might encounter unexpected problems along the way. You may run out of money suddenly. Maybe customers won't be willing to pay what you want. You must be ready to deal with such situations in order to survive.
One good tip is to set up a separate bank account specifically for your business. You will always know how much money you have coming in.
How do I get started with woodworking?
Building furniture is the best way to learn how furniture is made. While you will need tools, mistakes are inevitable, but you will learn the ropes if you persevere.
Start by choosing a project you'd like to complete. You can make a simple box or a large entertainment center. Once you've settled on a project find a local skilled woodworker. Ask him or her for advice on what tools you'll need and where to find them. It's possible to ask your friend if they do this type of work.
How do I choose the right tools for me?
It's important to consider your preferences and needs when buying tools. Do you prefer metal handles or plastic? What size nails and screws do you usually use? Are you comfortable with power tools, or would you rather use hand tools?
What is the difference between a hobbyist woodworker and a professional woodworker.
Hobbyists love making things from wood while professionals are more concerned with the quality of their work. Hobbyists often take pride in the creations they make and often share them to family and friends. Professionals will spend hours researching designs and then begin to create a project. They'll pay great attention to details, from choosing the most suitable materials to finishing the work perfectly.
Statistics
- Average lumber prices rose about 600 percent between April 2020 and May 2021. (familyhandyman.com)
- Woodworkers on the lower end of that spectrum, the bottom 10% to be exact, make roughly $24,000 a year, while the top 10% makes $108,000. (zippia.com)
- If your lumber isn't as dry as you would like when you purchase it (over 22% in Glen Huey's opinion…probably over 10-15% in my opinion), then it's a good idea to let it acclimate to your workshop for a couple of weeks. (woodandshop.com)
- Most woodworkers agree that lumber moisture needs to be under 10% for building furniture. (woodandshop.com)
External Links
How To
How do I accurately measure wood?
We have several ways to measure wood. We use a variety of methods to measure wood.
Two jaws can be opened and closed on a digital caliper. One jaw holds a measured object and the other measures distances between the points. The digital caliper is great for measuring small distances like thicknesses of wood.
Laser levels emit an infrared laser beam that projects a straight line across the floor. A red dot is created by the laser. You can check if the surface is level by looking down at the line. Large surfaces can be checked for accuracy with laser levels.
Bubble levels look similar to a compass. There is a bubble in the center of the device. As long the bubble is not in the middle, the device will show you whether the surface of the object is level. Bubble levels can be used for checking the accuracy in smaller areas.